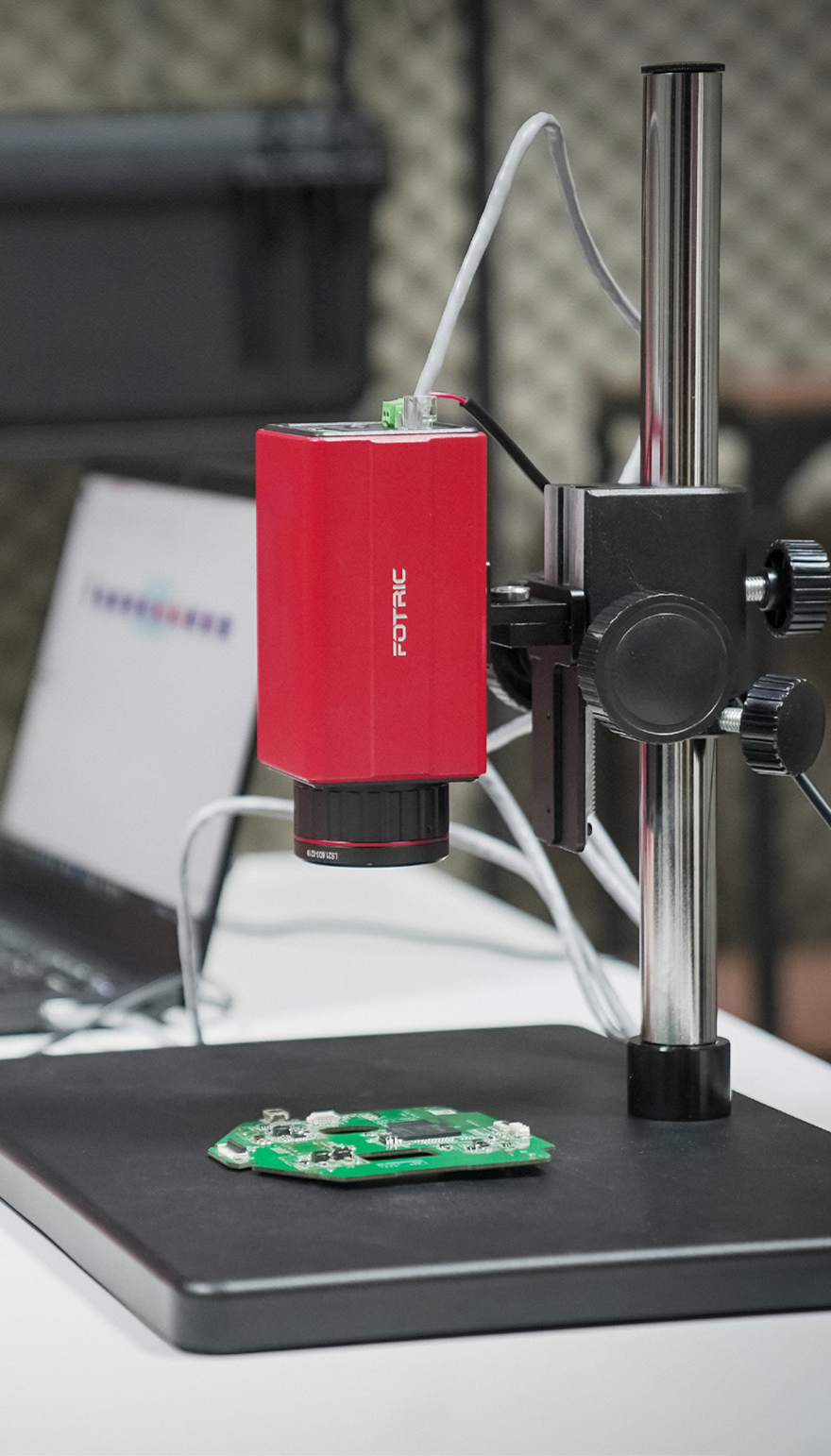
FOTRIC 600 R&D thermal camera test station solutions
Share
The FOTRIC 600 R&D thermal camera is a cutting-edge tool designed to meet the diverse needs of engineers, researchers, and product developers. Equipped with advanced hardware, including a high-resolution infrared camera, precision macro lenses, and robust PC software, the FOTRIC 600 provides powerful thermal imaging solutions for various industries. Whether you're working on electronics like printed circuit boards (PCBs), testing semiconductor dissipation, or conducting research in pharmaceuticals, this thermal camera delivers reliable results by identifying temperature anomalies and heat signatures.
Optimized for R&D and Engineering
The FOTRIC 600 thermal camera is specifically tailored for Research and Development (R&D) applications. With a thermal sensitivity of 0.03°C and resolution up to 640x480, this infrared camera can capture minute temperature changes in small components. The system also includes interchangeable lenses such as 20μm and 50μm macro lenses, ideal for micro-thermography, making it perfect for precise thermal imaging on miniature parts. A sturdy test bench enables users to start testing rapidly, and the infrared camera is capable of operating in environments ranging from -20°C to 650°C, maintaining accuracy even in extreme temperatures with a margin of ±2°C or ±2%.
Applications of FOTRIC 600 in Micro-Thermography
1. PCB Testing
In electronics, overheating is a common issue that can lead to product failure. The FOTRIC 600's thermal imaging capabilities can easily detect heat anomalies on PCB boards. By identifying areas with excess heat, such as faulty connections or defective components, the camera helps engineers rectify issues before they escalate. This infrared camera is critical for detecting hotspots, solder joint issues, and short circuits in both prototyping and mass production. It helps detect failures like hotspots, wonky temps, misinstalled chips, wiry issues, sneaky cracks, RF troubles, and bad soldering.Using infrared thermal imaging, engineers can ensure the quality of the PCB layout and detect problems like increased contact resistances, hidden cracks, or improperly mounted components. These issues, if left unresolved, could lead to malfunctions or reduced product lifespan. The FOTRIC 600’s PC software, AnalyzIR, captures real-time data, allowing for comprehensive heat analysis during the testing phase.
0s 6s 9s 17s
So, like, we totally found a glitch in the circuit board, it was like a hotspot or something! The whole heating process was like a drama queen, being monitored and recorded through FOTRIC AnalyzIR (Time: 0s, 6s, 9s, and 17s).
2. Chip heat dissipation analysis
One of the biggest challenges in modern electronics is managing the heat generated by increasingly compact devices. A poorly designed heat sink can significantly reduce the lifespan of a chip by allowing heat to accumulate, leading to failure. The FOTRIC 600 thermal camera excels in testing the dissipation of chips by measuring heat changes during different operational stages.

For example, infrared thermal imaging can monitor an LED chip during an automotive headlight test. If the heat sink is not functioning properly, the chip can reach dangerous temperatures, such as 120°C, which may trigger an automatic alert in the AnalyzIR software. By analyzing these changes, product developers can improve heat sink designs, thus extending the life of critical components.

3. Electronic products
In today’s miniaturized electronics, heat management is even more critical. The thermal camera can identify defects in components as small as those found in semiconductors, LED modules, and DC converters. For instance, during a post-production TV module aging test, the FOTRIC 600 detected an abnormal temperature of 93.8°C, a sign that the component would age prematurely and fail earlier than expected. Such precise detection allows manufacturers to address defects before products hit the market.

During the TV module aging test right after the manufacturing process, the temperature reached 93.8 ℃ unexpectedly which will result in rapid and premature aging and further caused a malfunction.
In another example, the FOTRIC 600 helped engineers identify faulty insulation in a universal prototype circuit board, preventing short circuits and subsequent product failure.

A faulty DC-to-DC converter is determined since the temperature reached 98.2 ℃ abnormally.
Car microphone PCB quality can be inspected by capturing the temperature distribution of the working circuit board and comparing it with the thermal field of a normal product to determine whether the product is defective. The left triode (blue box) plays a role in the first amplification stage, but it does not work in the defective product, meanwhile, the upper resistor and the right triode are slightly heated (purple box).

Normal car microphone PCB Defective car microphone PCB
LED beads are tested after the manufacturing process to help in quality control, and reasonable layout of heat-generating components, since local overheating due to poor dissipation shortens the LED life. In the figure, the non-uniform heat distribution of LED with high local temperature is discovered.

An 8-layer universal prototype circuit board is energized for testing and a short circuit occurred due to the faulty insulation of the board in the 2nd layer.
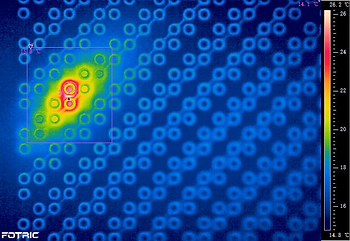
4. Biomedical and pharmaceutical testing
The FOTRIC 600 is also widely used in biomedical and pharmaceutical testing. In these fields, the thermal properties of materials often determine their effectiveness. Using the FOTRIC 600’s 50μm macro lens, researchers can evaluate the solar thermal conversion efficiency of nanomaterials or test pharmaceutical substances for heat anomalies, ensuring higher precision and more reliable data collection.

Detected by 50μm macro lens
5. Material testing
Material testing often involves measuring how materials respond to changes in temperature, tension, or stress. The FOTRIC 600 thermal camera provides real-time monitoring of temperature changes in fibrous materials under stress, helping researchers better understand material performance. In addition, it can measure the thermal conductivity of different substances, ensuring that components meet the necessary standards for thermal efficiency and durability.
With powerful PC software, 600 R&D thermal cameras can test the performance through temperature changes of fibrous carbon material subjected to tension.

And test the thermal conductivity of two materials (two bars) as well.

Why Choose FOTRIC 600 for R&D?
The FOTRIC 600 infrared camera stands out due to its combination of high sensitivity, multiple lens options, and advanced PC software for detailed analysis. With a thermal sensitivity of 30mK, the camera provides high-resolution thermal data, ensuring that even the smallest temperature changes are detected. The full radiometric video stream offers frame rates of up to 30Hz, allowing for real-time monitoring and recording of tests.Key benefits include:- 20μm and 50μm macro lenses for micro-thermography applications.
- High thermal sensitivity of 30mK.
- Wide temperature measurement range (-20°C to 650°C).
- Advanced PC software for in-depth thermal analysis.
- Accurate measurement with an error margin of ±2°C or ±2%.
Conclusion
The FOTRIC 600 R&D thermal camera offers an all-in-one solution for industries that rely on precise thermal data. From PCB board testing to chip dissipation and pharmaceutical research, its thermal imaging technology allows for comprehensive heat monitoring across a variety of applications. With its robust design, interchangeable lenses, and user-friendly PC software, the FOTRIC 600 is a must-have tool for engineers and researchers alike.
If you're looking to invest in a versatile and high-performance infrared camera for R&D purposes, the FOTRIC 600 is an excellent choice. Explore more about its capabilities by visiting NovaTestPro.com or contacting info@NovaTestPro.com for any inquiries.